Flotation processes are used to separate solids from a liquid (e.g. water). The flotation process most commonly used in water treatment is dissolved air flotation.
The suspension to be treated (raw water) is placed in a tank. Flocculation chemicals can be added to the raw water in order to improve the flotation of the contaminants. A pump transports the raw water, which enters the flotation column via a vertical pipe. The height of the supply line can be adjusted.
A water circuit with pump is connected to the flotation column. At the highest point of the circulation there is negative pressure. The required air for the flotation is sucked in by opening a valve located at this point. The air dissolves in the water under pressure. Part of the water flows back to the pump via a bypass. The other part of the water enters a pressure vessel filled with Pall rings. The pressure vessel ensures a sufficiently long dwell time to dissolve the air and to separate undissolved air.
The water then enters the flotation column from below via a valve. This causes a sudden drop in pressure to almost atmospheric pressure. Since the solubility of air increases with increasing pressure, the excess air forms small bubbles. The air bubbles accumulate on the contaminants. The contaminants rise up in the column together with the air bubbles. At the upper end of the flotation column, the contaminants enter a circulating channel. The treated water is taken from the bottom of the flotation column and collected in a tank.
The pressure and the flow rate of the circulation can be adjusted. Flow rate, temperature and pressure are measured and displayed.
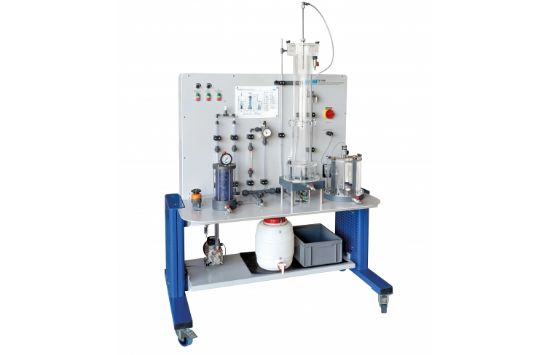