Absorption is used to remove one or more gaseous components from a gas flow using a solvent.
First of all, a CO2 and air gas mixture is produced. It is possible to adjust the mixing ratio using valves. The flow rates of the gas components are displayed.
A compressor delivers the gas mixture into the lower section of the absorption column. In the column, part of the CO2 is separated in the counterflow with the solvent. Water is used as the solvent. The CO2 is absorbed by the downward flowing water. To separate the absorbed CO2, the charged water is then fed from the lower section of the absorption column into a desorption column. As the pressure is reduced and the temperature is increased, the solubility of the CO2 falls. A heater heats the water. A water jet pump generates negative pressure in the desorption column and causes the CO2 gas to be emitted from the water. A pump then delivers the regenerated solvent back into the absorption column.
The water temperature can be controlled. Flow rate, temperature and pressure are continuously measured. The two-section column is equipped with connections to determine the pressure losses. The pressure loss in the respective sections can be displayed via two U-tube manometers. To evaluate the success of the process, the trainer includes outlets for taking gas and liquid samples. The gas samples can be analysed using the hand-held measuring unit supplied.
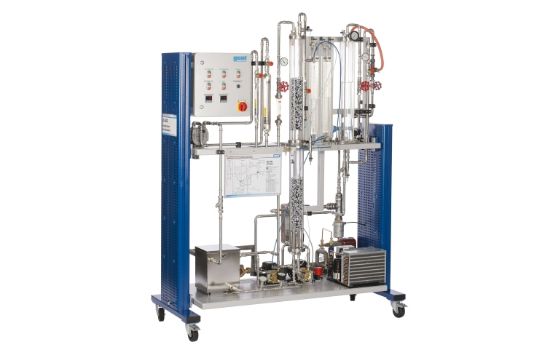